We love robots—but we love talking to people even more.
Equipment acting up? Line at a standstill? Or just need to talk it out? Our expert support team is one call or email away—real help from real humans, fast.
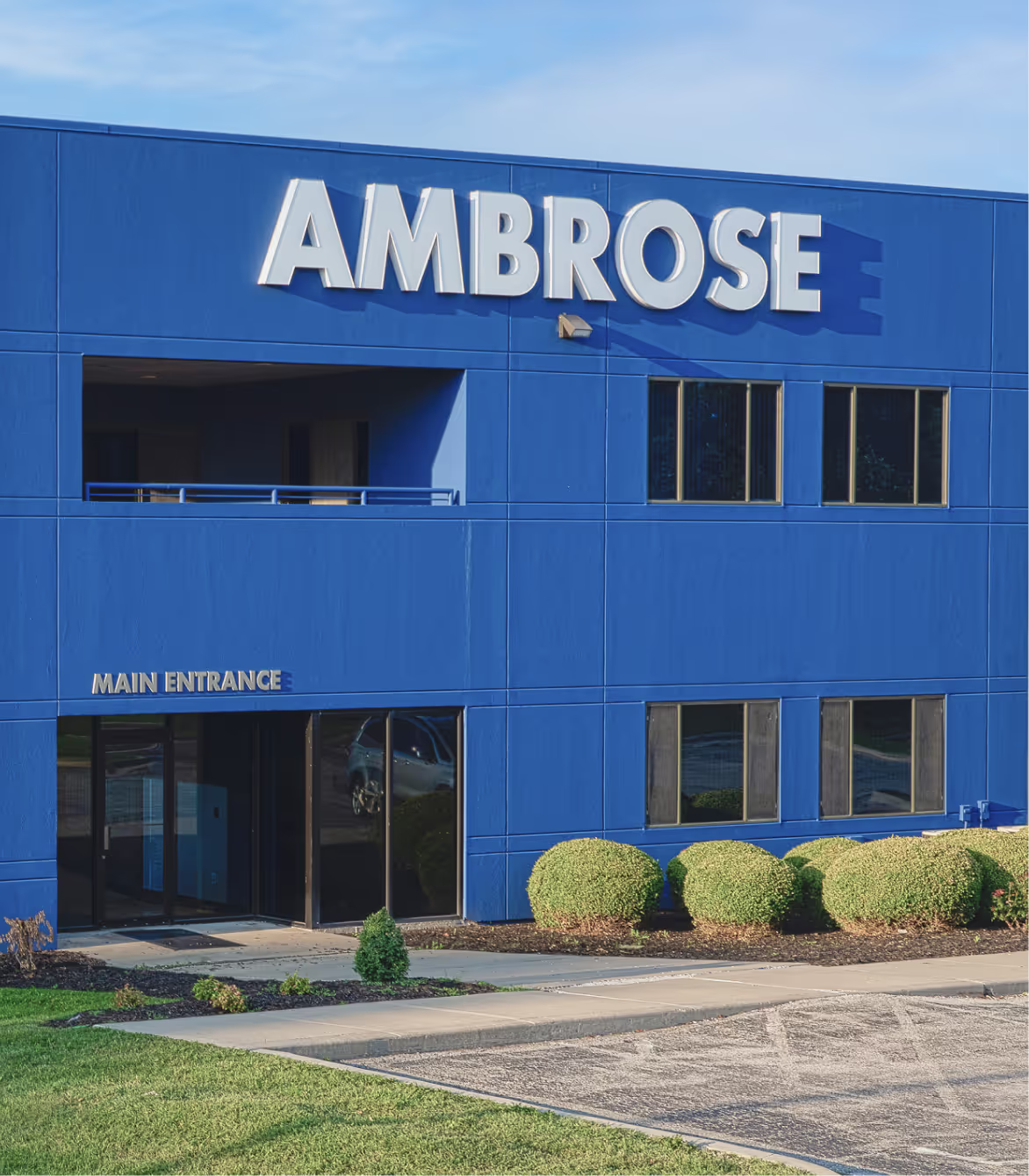
Let’s chat
Need a quote, service support, or just not sure where to start? Tell us what’s going on—we’ll jump in and figure it out together.
Customer Support
Talk to the right people
Here for the long haul—supporting everything from urgent repairs to system-wide improvements.
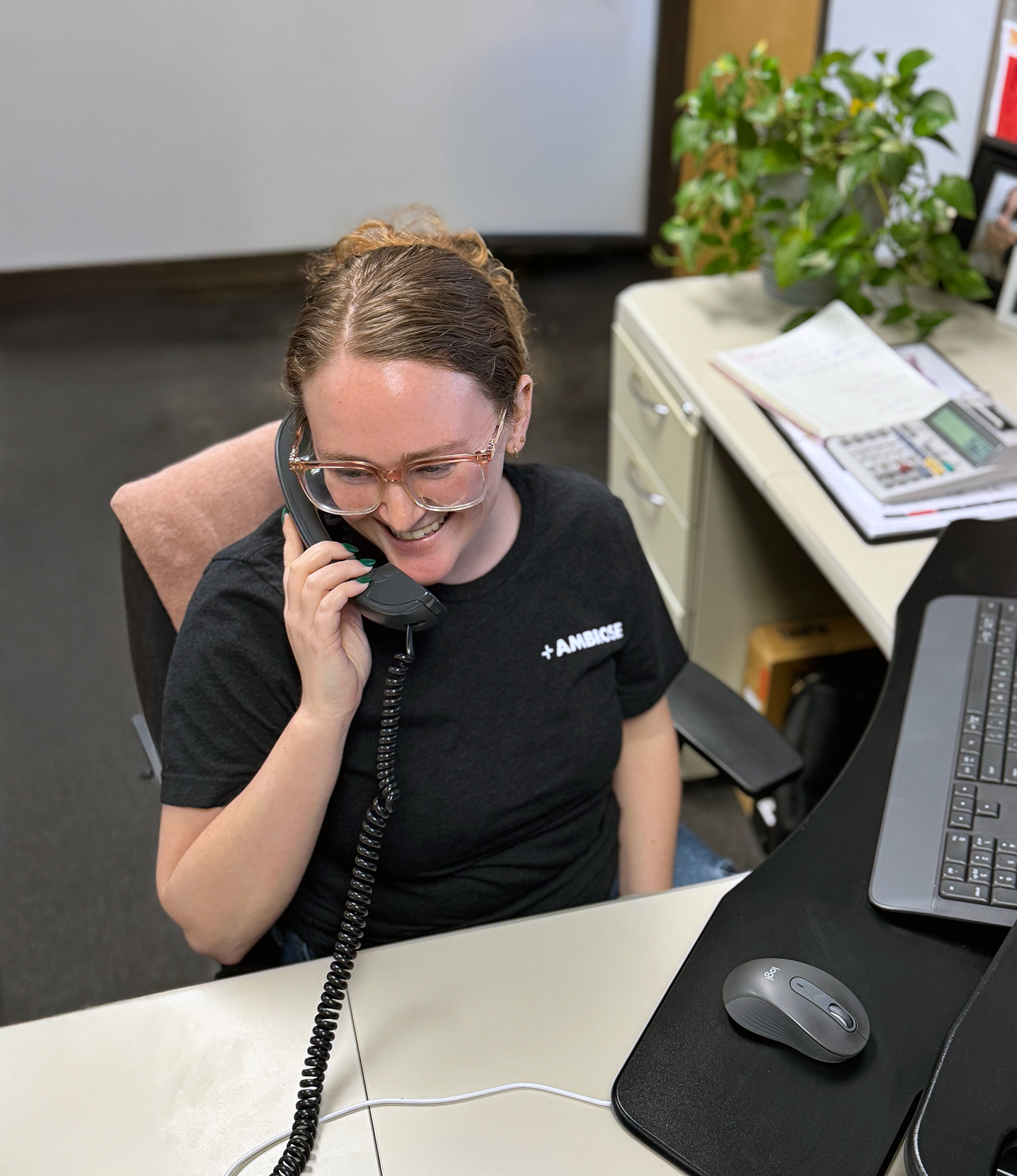
Customer Support
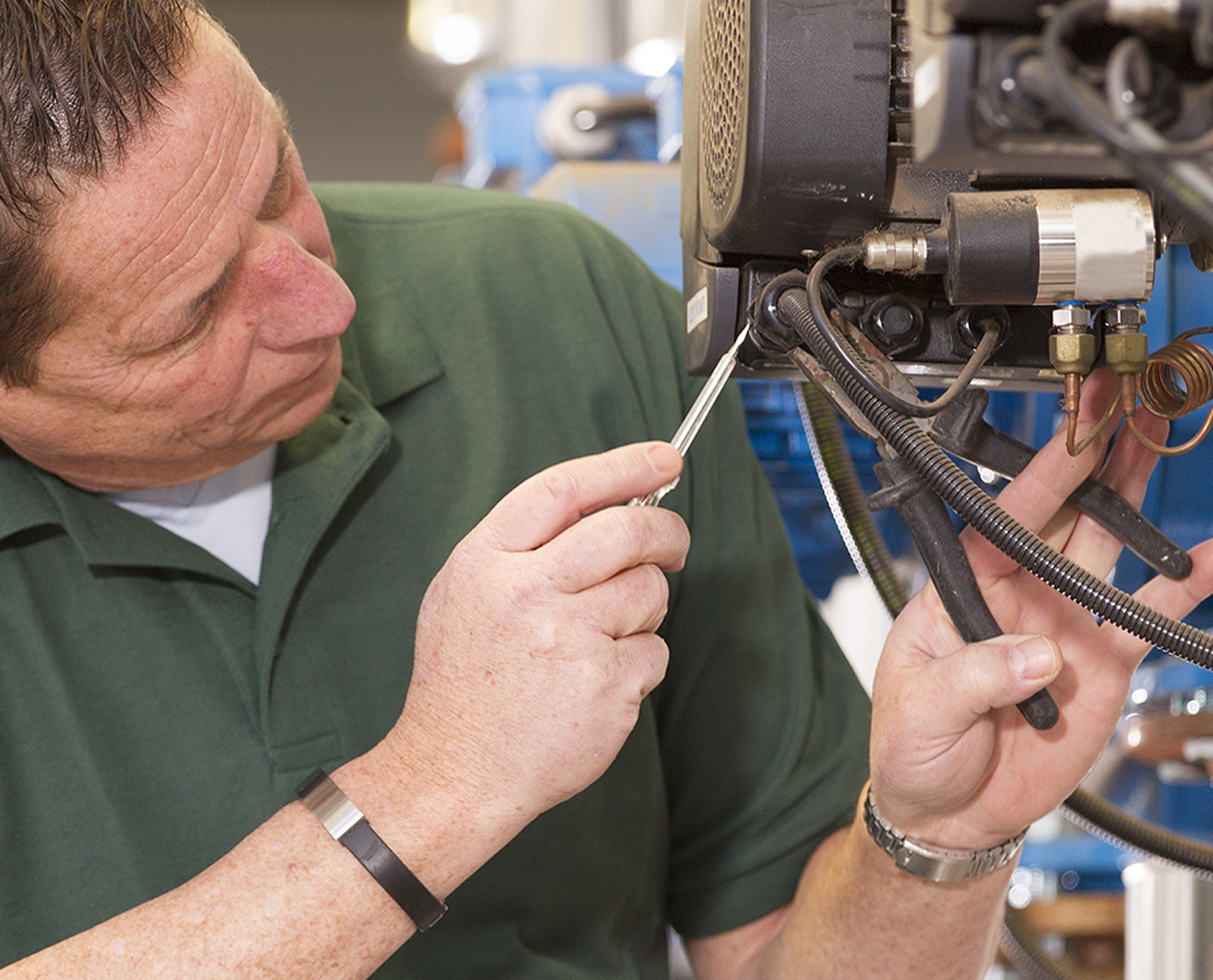
Service
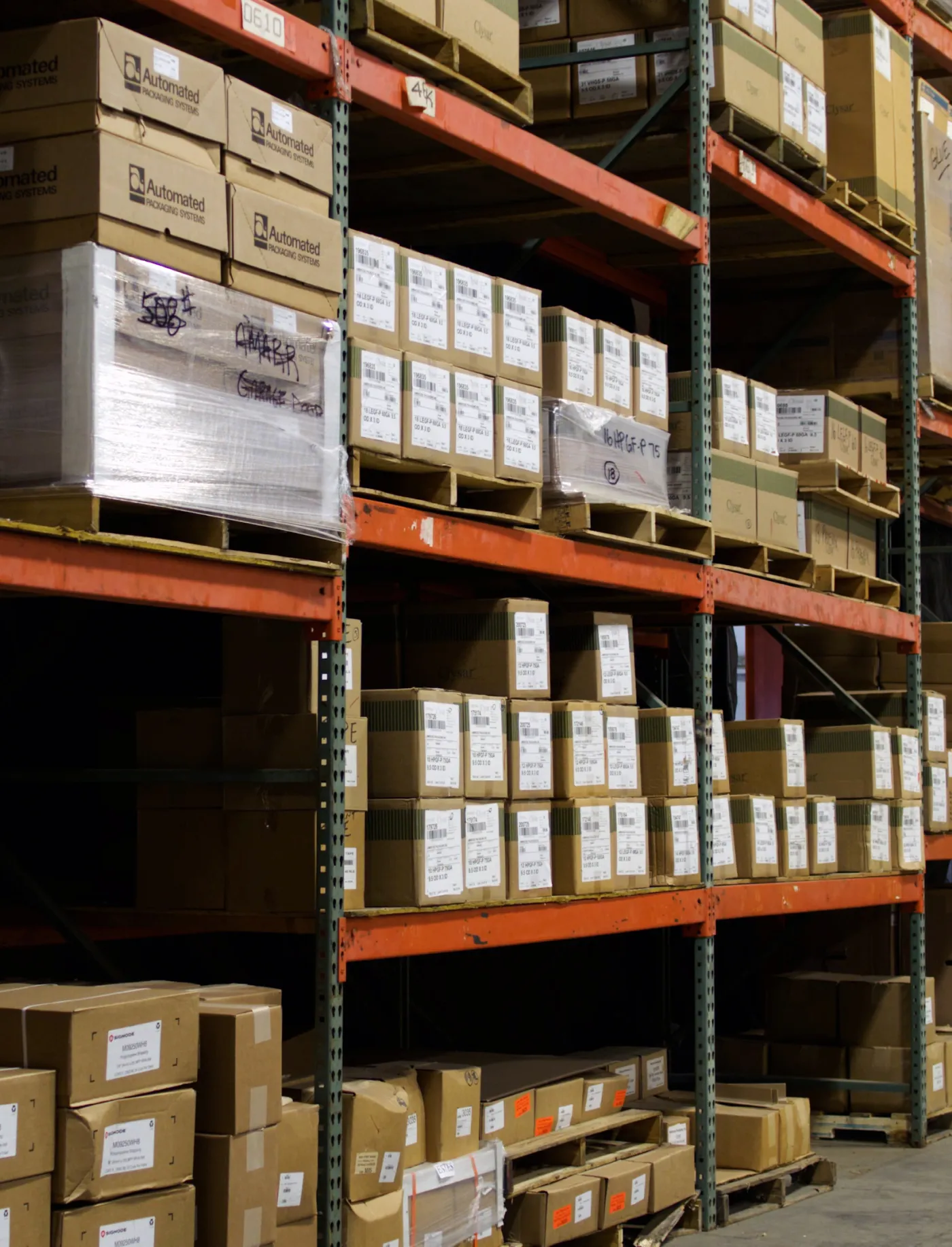
Parts & Supplies
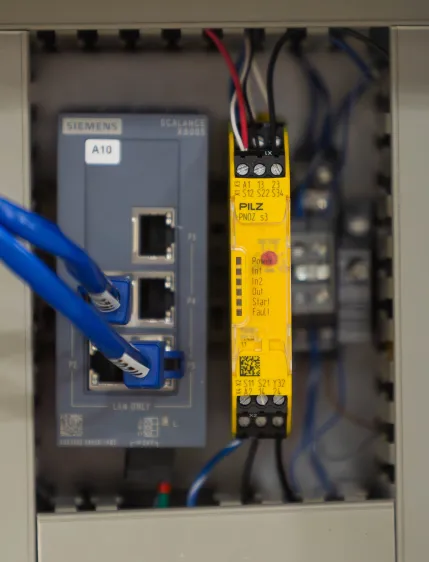
Engineering Services
Frequently asked questions
What does Ambrose do, exactly?
Do you offer turnkey systems or individual machines?
What’s the typical timeline for a new system?
How does the project process work?
Before shipment, we conduct thorough factory acceptance testing (FAT) using your actual product to validate system performance and ensure it meets all expectations.
Certified technicians and a dedicated project manager oversee installation and startup on-site—ensuring everything is integrated, tested, and production-ready. This is followed by hands-on operator training and scheduled optimization visits to fine-tune performance post-launch.
Long after startup, our technical service team and extensive in-house parts inventory support your operation with preventative maintenance, fast-response troubleshooting, and long-term reliability planning.