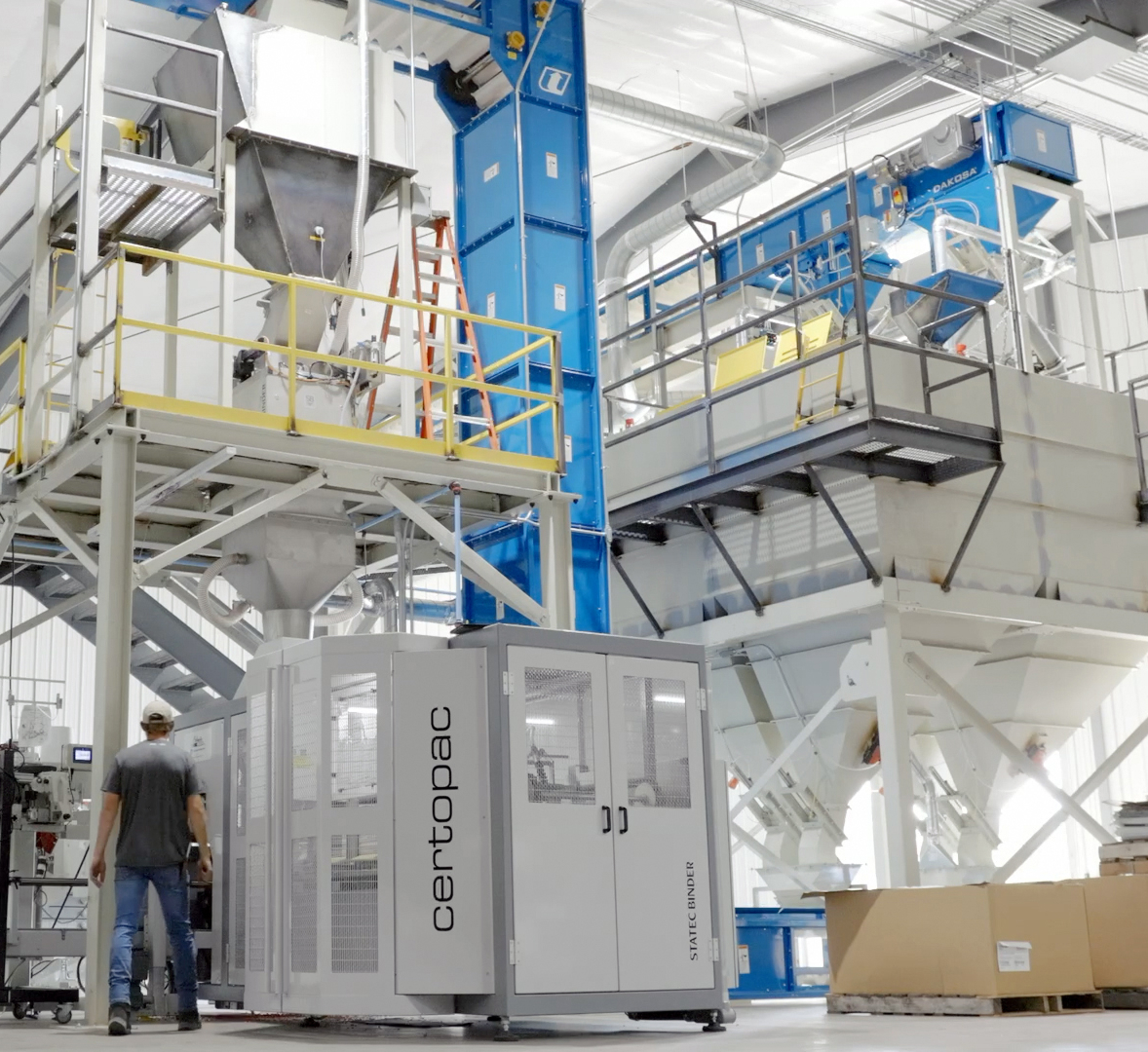
OVerview
Bulk Solids Handling & Filling
From powders to pellets to feed, our systems are built to move product efficiently, weigh with precision, and package consistently. Integrated elevators, conveyors, feeders, and automated bagging solutions help you sustain throughput, reduce spillage, and hit spec—batch after batch.
Start a project
Start a project
Start a project
Applications
Adaptable by design
We engineer every solution with flexibility in mind—designed to handle everything from 50lb bags to super sacks, adapt to changing production demands, and deliver consistent results across materials, packaging formats, and throughput requirements.
Hanging-weigh frames support 2- and 4-loop “super sacks” from 500 lb to 2 ton. Inflatable neck seals, densification vibration, and automatic loop release create square, transport-stable bags every cycle.
Typical applications include: food, chemical and mineral products.
Typical rate: 15–40 bags/hr depending on weight and densification cycle.
Pre-made multiwall paper, laminated woven polypropylene or polyethylene bags (2-110 lb) are manually placed or automatically placed, filled, and sealed. Servo-driven net-weigh scales offer high speed and high accuracy.Vertical or horizontal form fill and seal machines automatically form and weld plastic bags from roll stock and are capable of speeds ranging from 20 to 40 bags per minute.
Typical Applications: agricultural, seed, feed, chemical, pet food, human food, pharmaceutical, mineral products, ranging from fine powder, granules, pellets and even course materials such as decorative stone or charcoal.
Rates range: 2 to 40 bags/min depending on product and equipment choices
Net-weight lances top-, sub-, or bottom-fill steel or plastic drums and totes with liquids, slurries, or free-flowing powders. Automatic lance height, drip cups, and gas-purge options meet stringent chemical and food safety codes.
Best for: lubricants, coatings, flavors, pharma intermediates, hazardous chemicals.
Typical rate: 60–120 drums/hr or 15–25 totes/hr, semi- or fully-automatic.
- Sew & Tape – Fold-over or pinch‐style sewing heads apply crepe tape or glue for sift-proof seams on paper, poly-woven, or laminated bags.
-
- Heat & Ultrasonic Seal – Hot-air, impulse, or ultrasonic bars weld polyethylene liners or fully plastic bags for an airtight finish.
For powders, granular or pelleted products. Valve packers fill through a self-sealing sleeve or sleeves that can be sealed with ultrasonic welds. Valve bag packers are offered either as air packers or auger packers depending on the application.
Typical applications include: cement, lime, carbon black, cocoa, PVC resin.
Typical rate: 2-8 bags/min per spout; add spouts for higher output.
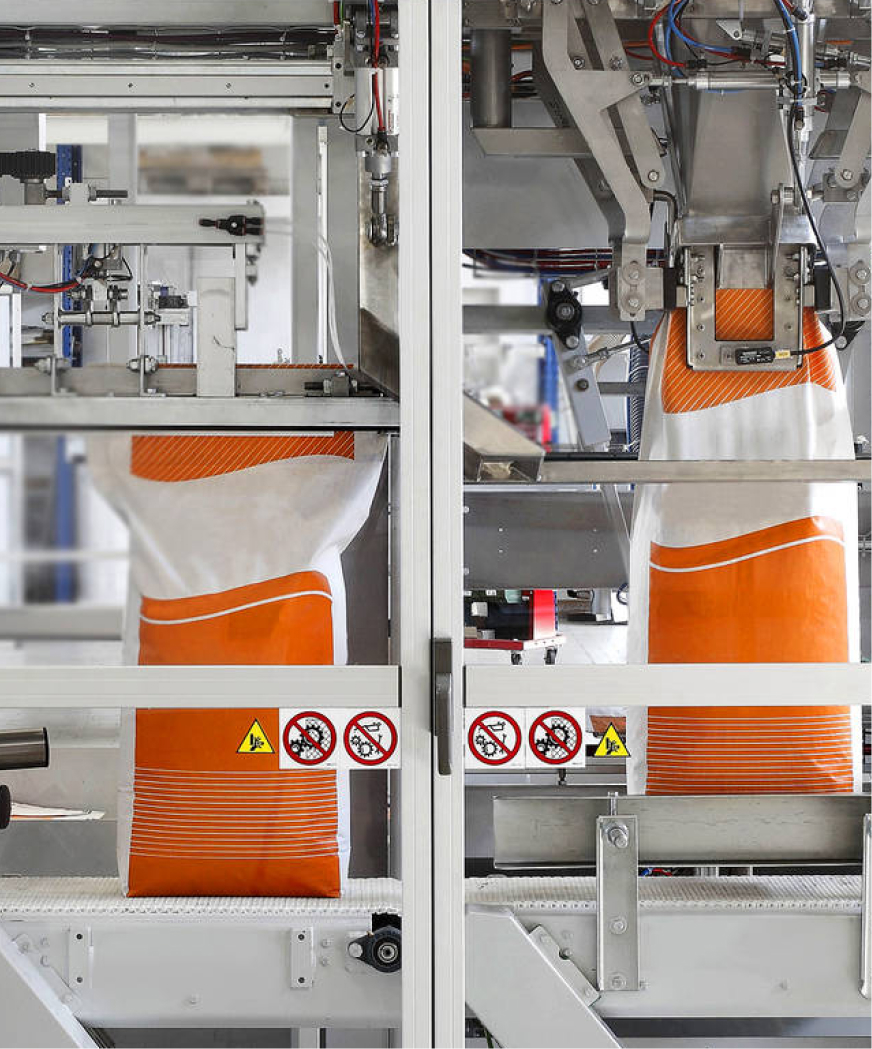
in the real world
Imagine your facility in action
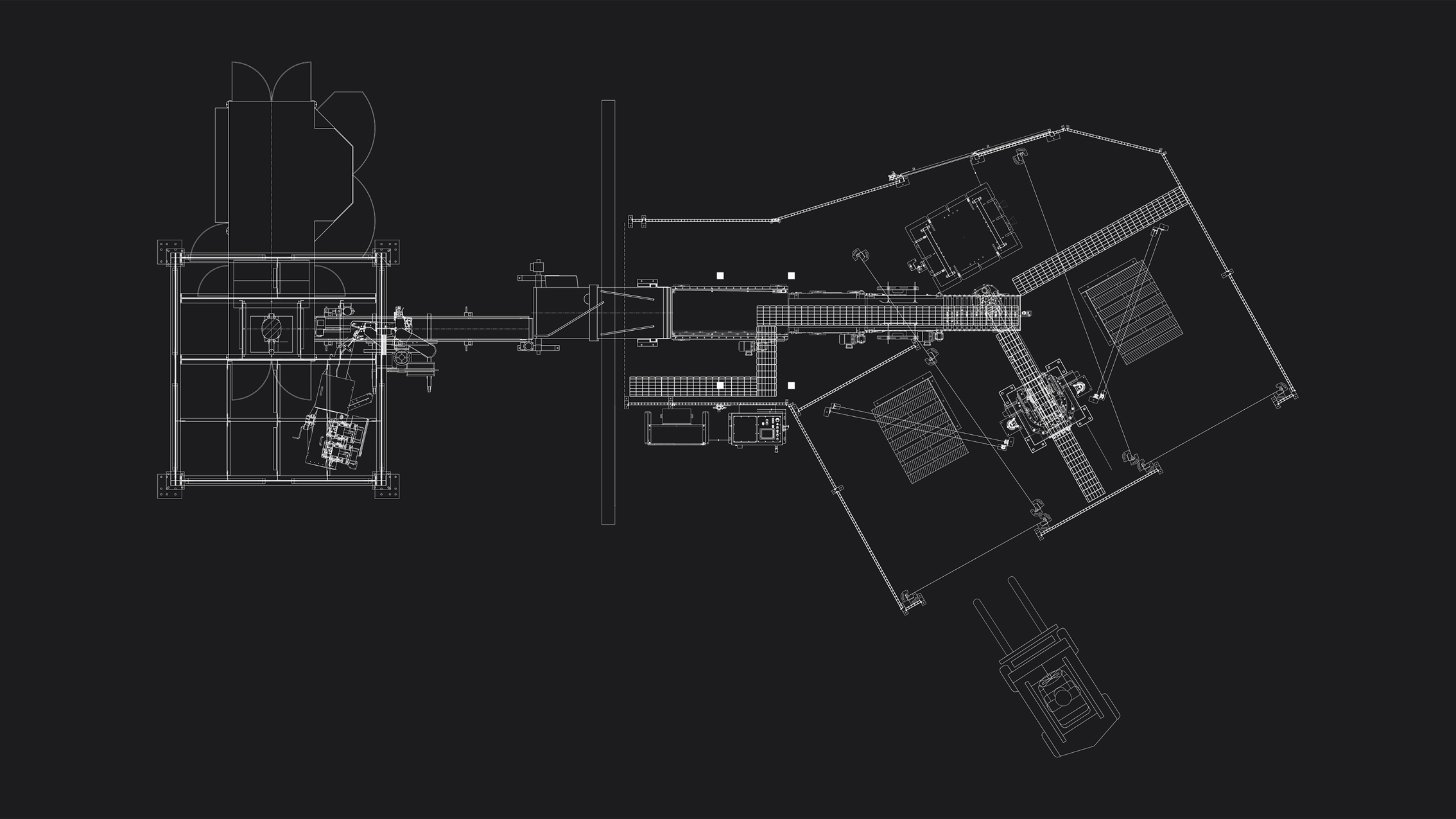
In this system
Bag Closing Conveyor
Bag Sewing System
Dual Tag Inserter
Fully Automatic Bagger
Knockdown Turner
Net Weigh Scale
Robotic Palletizing Cell
Benefits
Turn throughput into ROI
Integrated bulk-solids handling reduces labor, controls yield, and ensures consistent quality—maximizing value every shift.
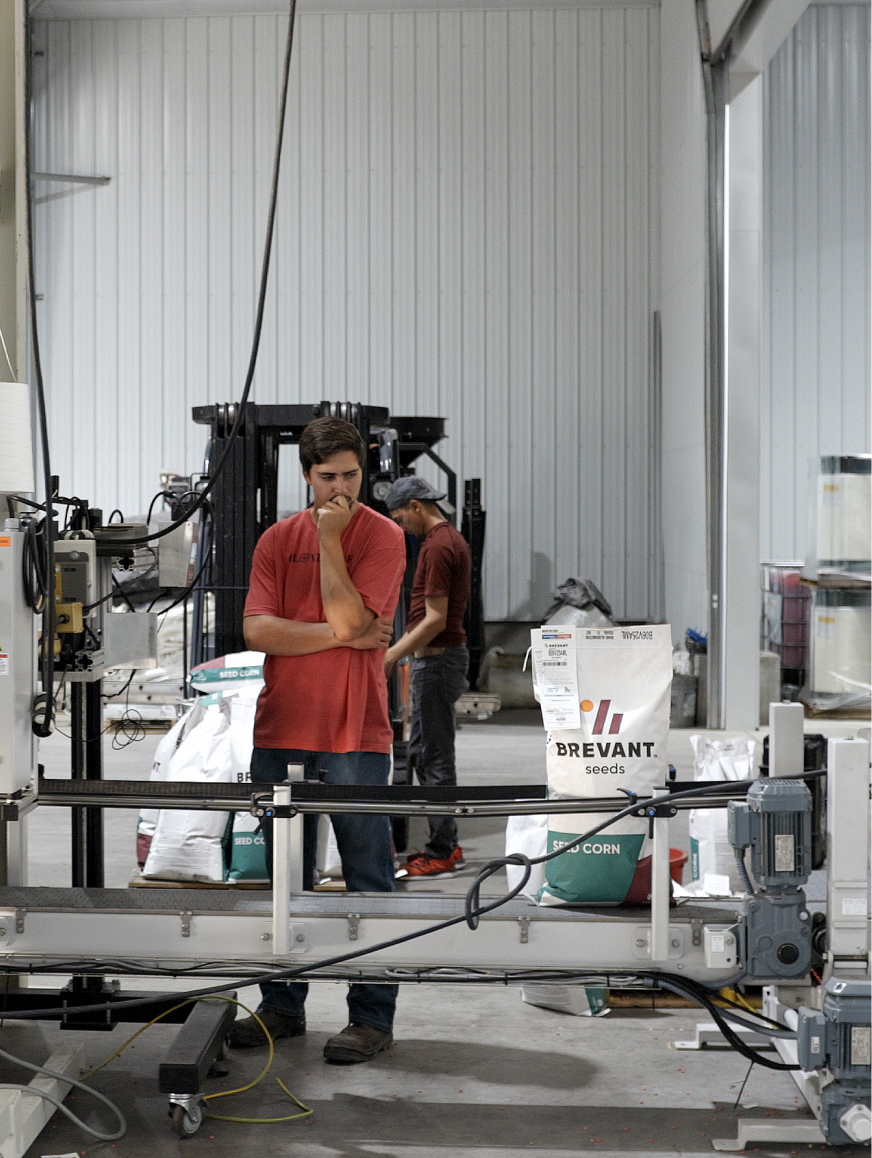
Consistent quality
Automated bagging delivers consistent fills, secure seals, and precise weight control—ensuring every bag meets your quality standards, run after run.
Cost savings
Bagging automation reduces labor costs, improves fill accuracy, and cuts rework—delivering consistent, measurable savings shift after shift. It’s a smarter way to boost efficiency and protect your bottom line.
Increased efficiency
Bagging automation streamlines throughput, reduces downtime, and improves consistency—driving greater production efficiency in your plant. It's how leading operations stay fast, focused, and competitive.
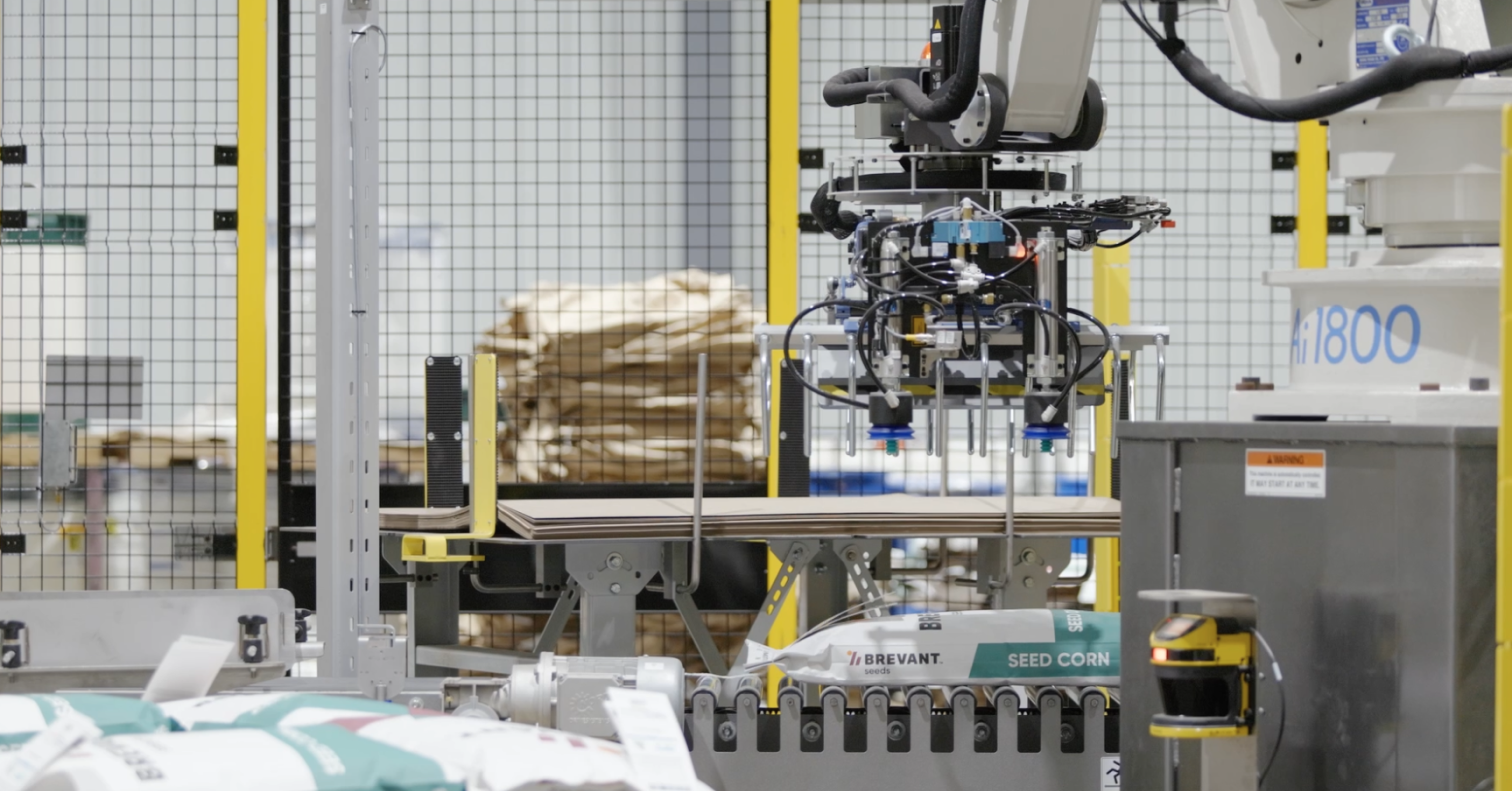
Project
Precise processes for seed bagging line
We replaced manual, outdated processes with an advanced automation system integrating robotics, intelligent sensors, and real-time monitoring. Our solution streamlined grain handling, minimized errors, and reduced safety risks while scaling to meet higher demand. As a result, the company's operations became significantly more efficient, with minimal downtime.
Check it out →
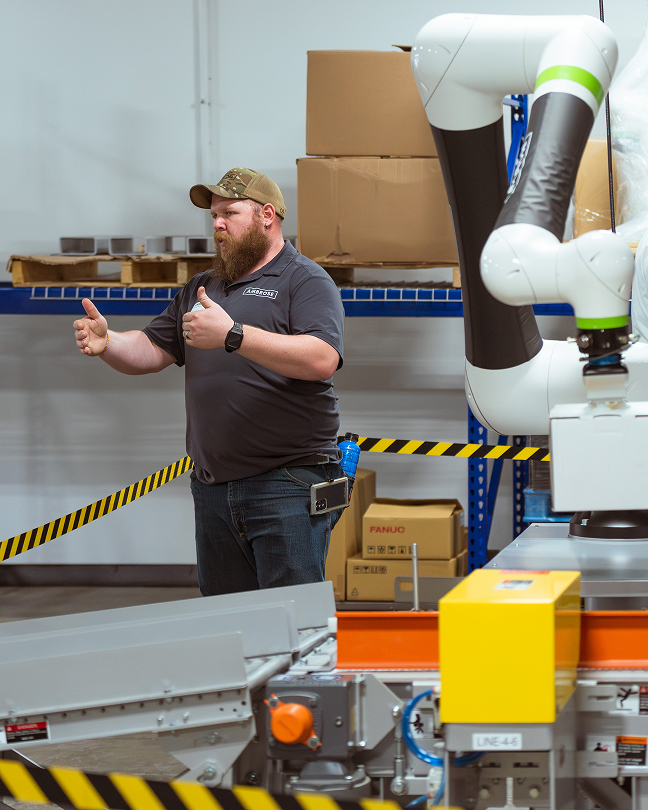
Let’s turn challenges into opportunities!
Whether you’re looking for equipment or to build a full line, we’d love to chat.
Support
Helping you where you need it most
Whether it's through expert advice, personalized solutions, or ongoing assistance, we are here to empower you every step of the way.
Parts & Supplies
Learn more
Learn more
Learn more
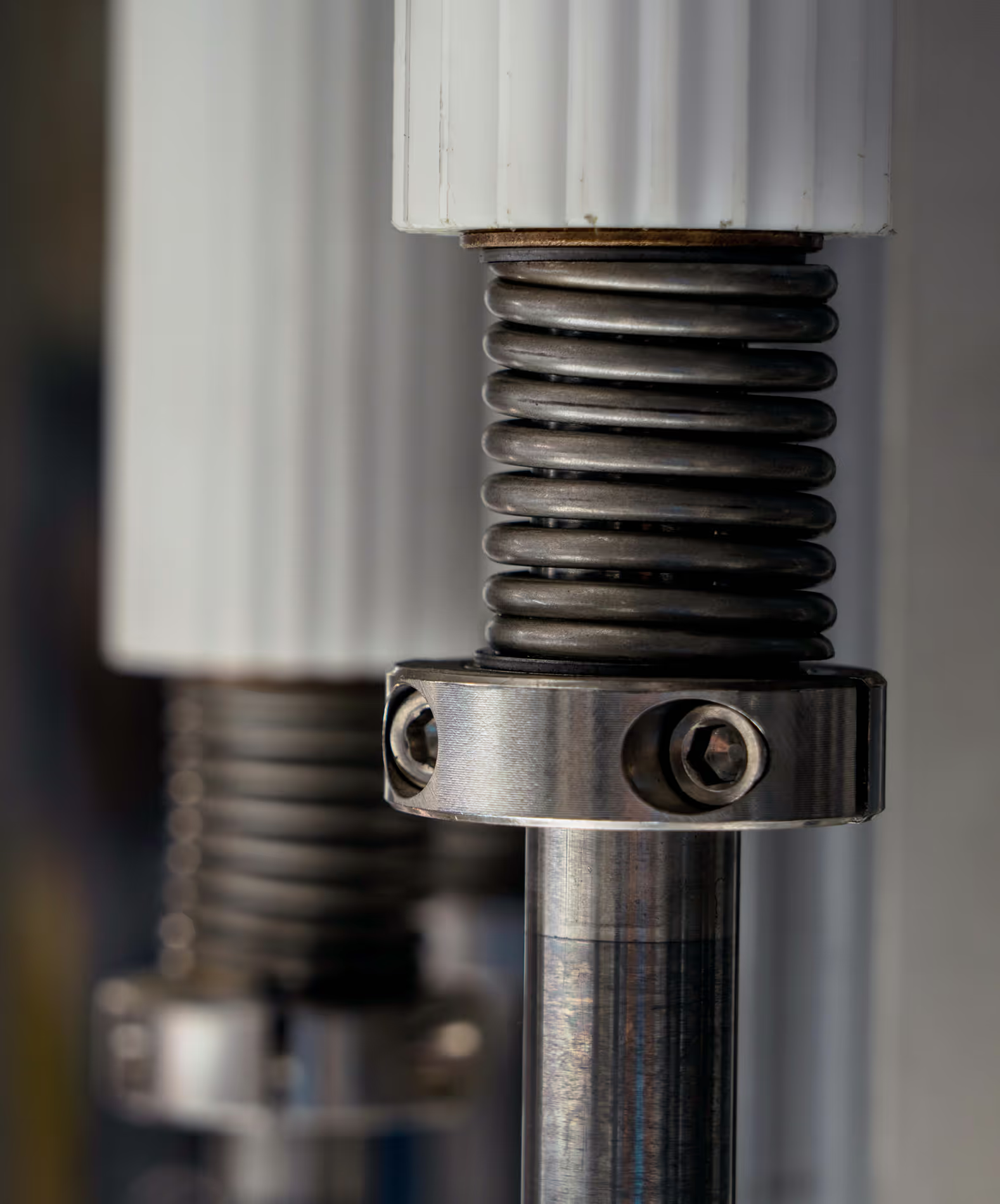
Engineering Services
Learn more
Learn more
Learn more
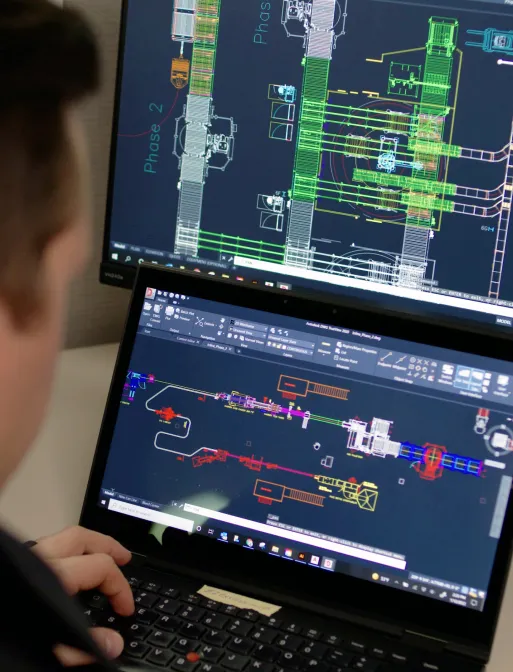