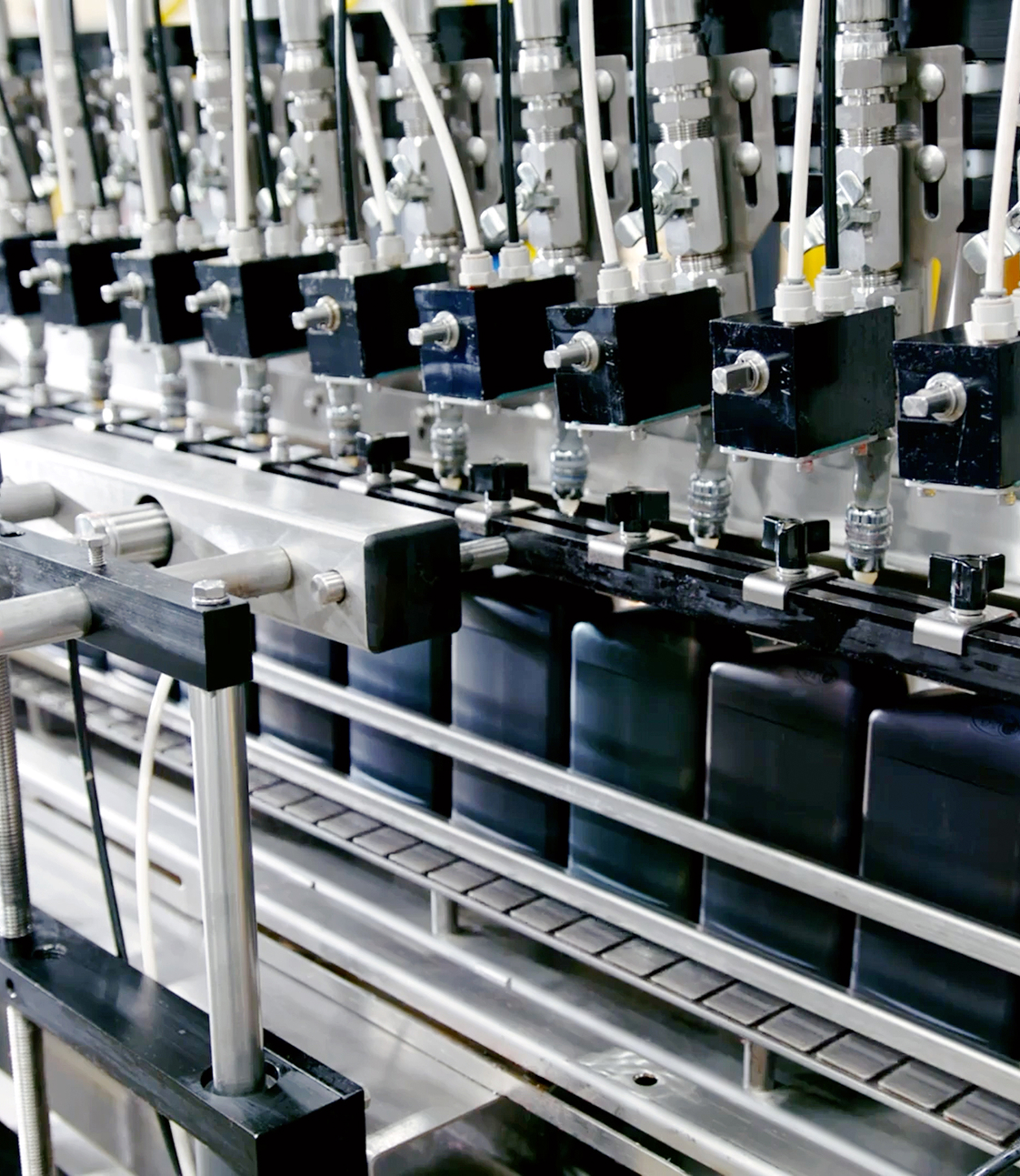
OVerview
Liquid Filling & Dosing
From thin to viscous—even hazardous—liquids require precise handling. We engineer filling systems to meet your product’s viscosity, hygiene standards, and production rates, then integrate upstream and downstream equipment to ensure every container is accurately filled, sealed, and ready for final packaging.
Start a project
Start a project
Start a project
Applications
Smarter liquid filling starts here
Integrated filling and capping systems reduce rework, boost throughput, and protect product integrity.
Inline, Rotary, Turrett, and single-head, pump & trigger inserter/placers
Rotary, inline, and monobloc applications
Unscramblers, Depalletizers, Tabletop Conveyance, Laning and accumulation
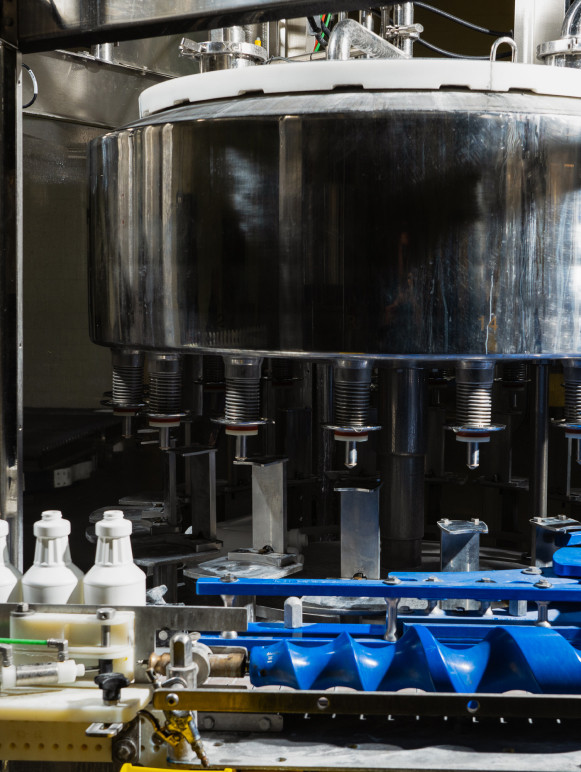
in the real world
Imagine your facility in action
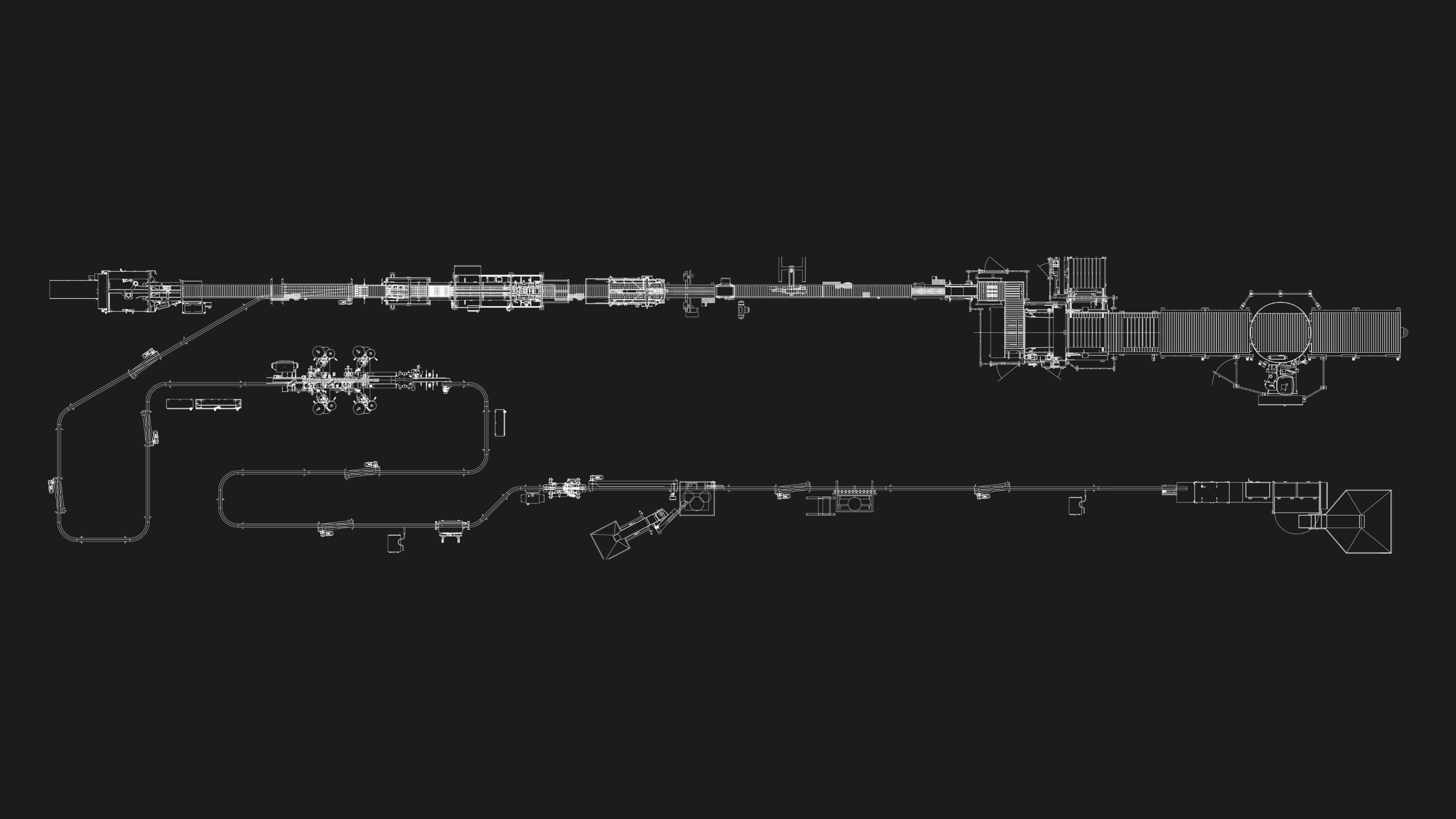
In this system
Automatic Stretch Wrapper
Capper
Case Check-Weigh
Case Erector
Case Labeler
Case Packer
Case Sealer
Conventional Palletizer
Filler
ICS (Interlocked Controls System)
Induction Sealer
Marking & Coding
Product Check-Weigh
Product Labeler
Unscrambler
Benefits
Precision fills, reliable results
Integrated liquid filling and inspection systems ensure accurate fills, consistent quality, and real-time defect detection—keeping your product on spec and your line running smoothly.
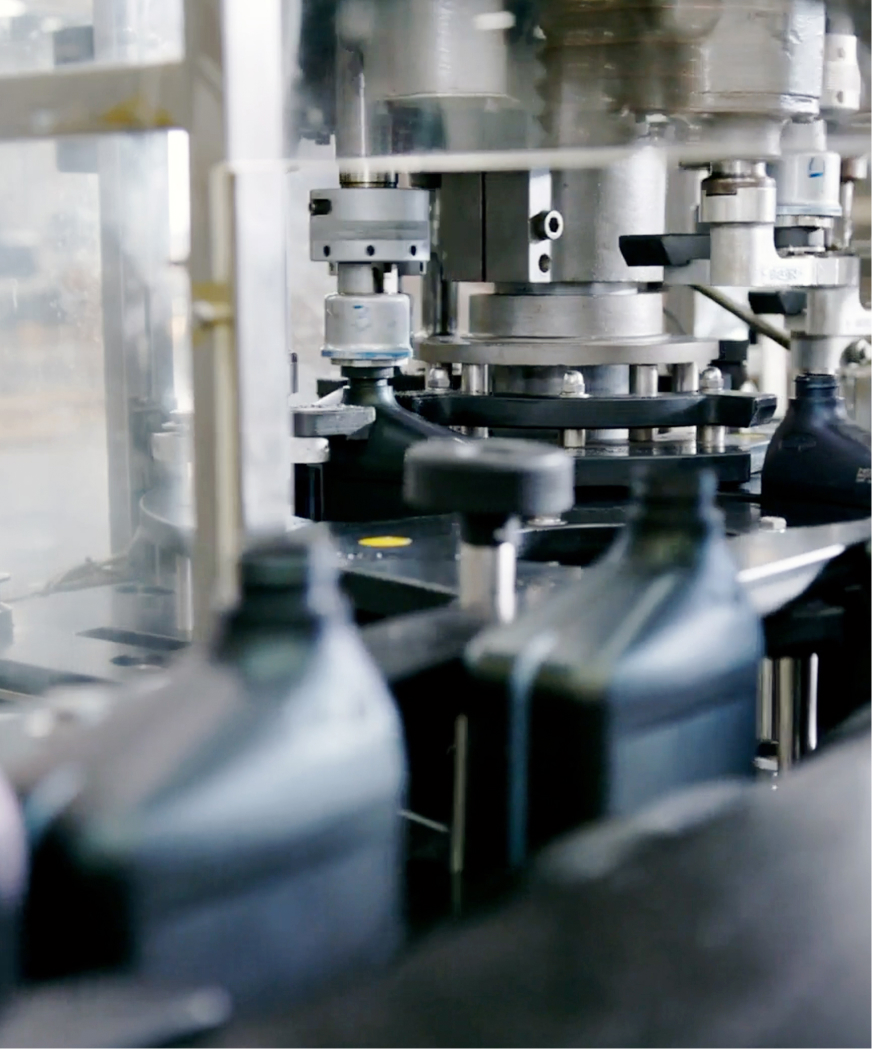
Built for speed
Throughput may be relative—but if it’s your benchmark, our high-speed liquid filling solutions are engineered to deliver. Designed for precision, uptime, and repeatable performance, they help you maximize output without sacrificing reliability.
Seamless integration
Boost production efficiency without a complete overhaul—by upgrading key components and automating critical points along the line, we help you get more from what you already have.
Wide product variation
Designed for flexibility—our systems support short runs, rapid changeovers, and varied product formats, making them ideal for co-packers, CDMOs, and manufacturers managing high SKU counts or frequent client-specific configurations.
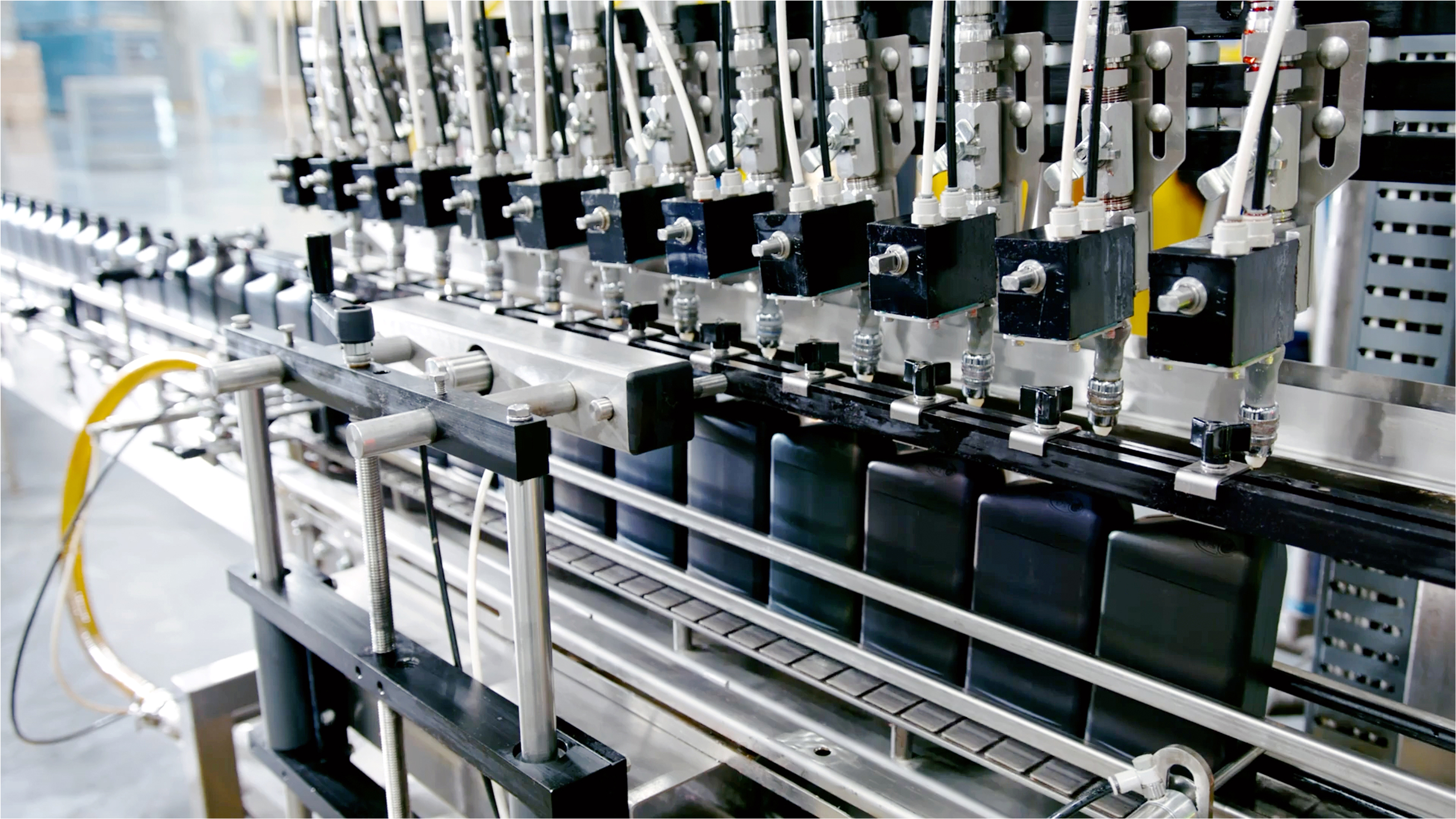
Project
End-to-end solution powers automotive-additive production
A fuel-additive plant needed a fast, cost-effective packaging solution for a Class I, Division 1 (C1 D1) area. By integrating pre-owned and new equipment into a fully automated, explosion-proof line, we met hazardous-location codes, minimized capital costs, and completed startup in just 10 months—boosting production with minimal labor.
Check it out →
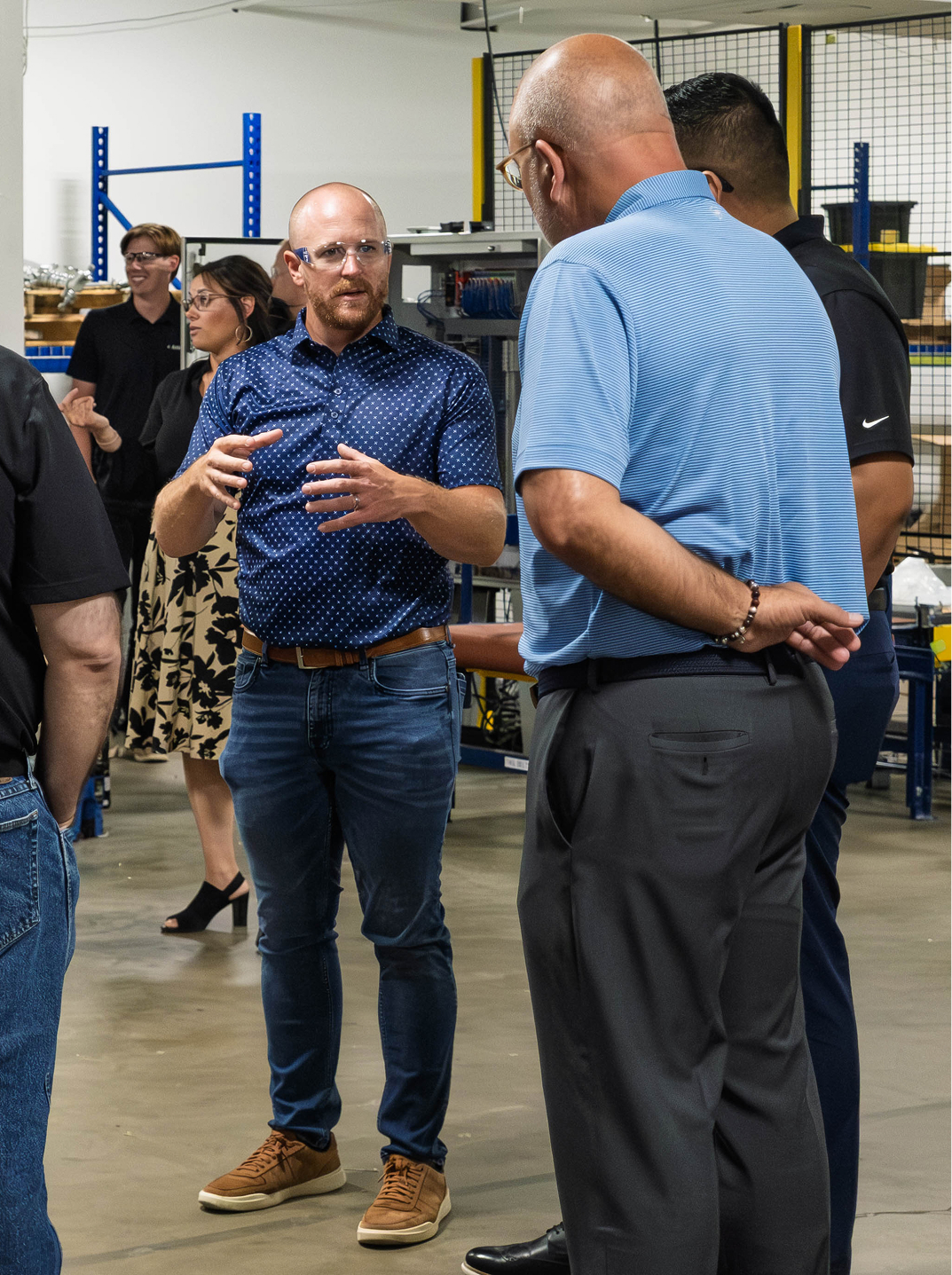
Let’s turn challenges into opportunities!
Whether you’re looking for equipment or to build a full line, we’d love to chat.
Support
Helping you where you need it most
Whether it's through expert advice, personalized solutions, or ongoing assistance, we are here to empower you every step of the way.
Parts & Supplies
Learn more
Learn more
Learn more
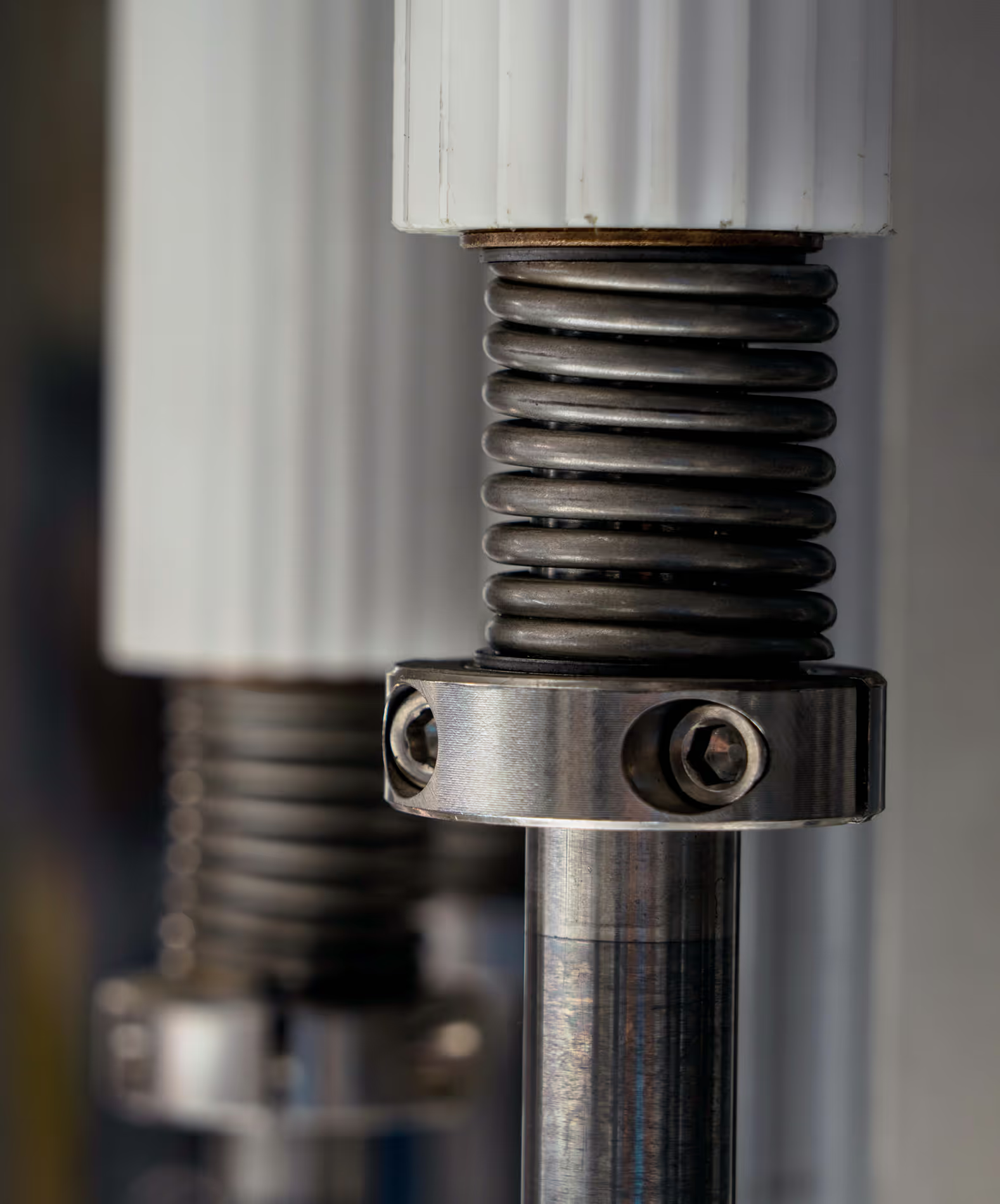
Engineering Services
Learn more
Learn more
Learn more
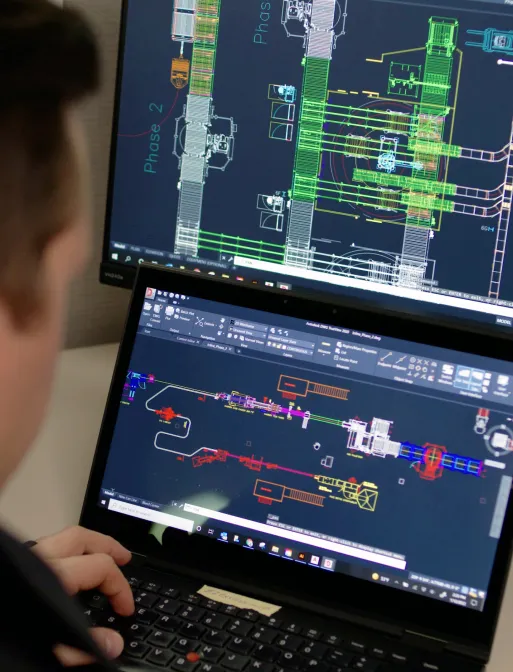