Automotive Additives Manufacturer
End-to-end solution powers automotive-additive production
El Dorado, Kansas
2023
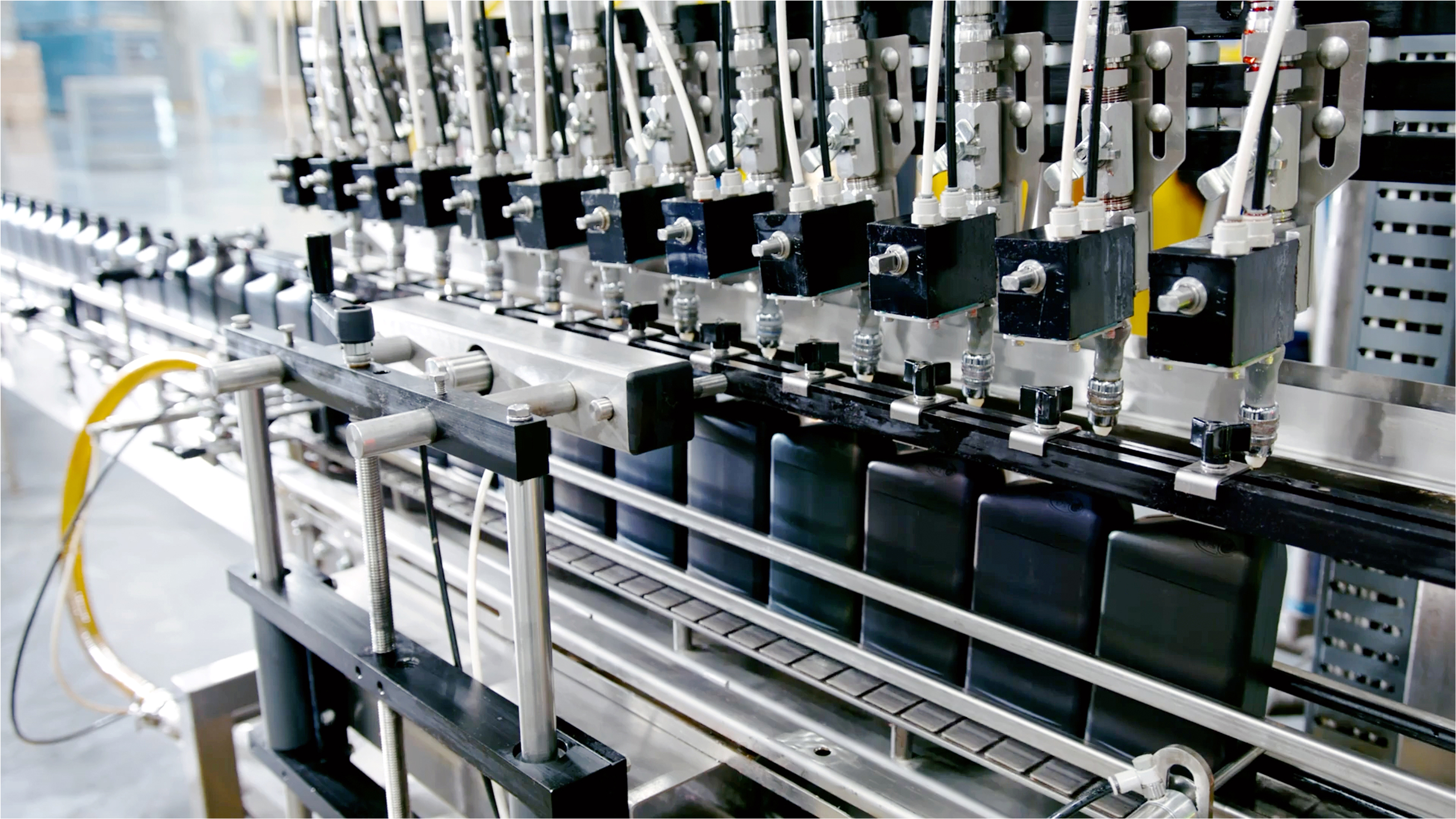
overview
Used & new assets for a rapid, compliant launch
Equipment Used
Apply-Only Product Labeler
Automatic Stretch Wrapper
Bottle Unscrambler & Orienter
Case Checkweigher
Case Drop Packer
Case Erector
Case Inkjet Printer
Case Sealer
Continuous Inkjet Printer (CIJ)
Conventional Palletizer
Induction Sealer
Inline Bottle Checkweigher
Inline Filler
Integrated Control System (ICS)
Laser Coder
Lineshaft Case Conveyor
Print-and-Apply Case Labeler
Remote HMI Panel
Rotary Capper
Tabletop Conveyor
An automotive-additive plant needed a turnkey, end-to-end liquid filling and packaging line—designed to handle everything from empty bottle infeed to a fully unitized, palletized load ready for shipment.
By integrating pre-owned and new equipment into a fully automated, explosion-proof line, we met hazardous-location requirements, minimized capital costs, and completed startup in just 10 months—boosting production with minimal labor.
The system included material handling, precise filling, capping, labeling, case packing, palletizing, and load containment—all seamlessly integrated for efficient, high-throughput operation.
IMPACT
Key results at a glance
10-month lifecycle
From purchase order to production.
C1 D1 compliant
System rated for flammable vapors at filler and capper zones.
Operators redeployed
Manual tasks limited to material replenishment after automation
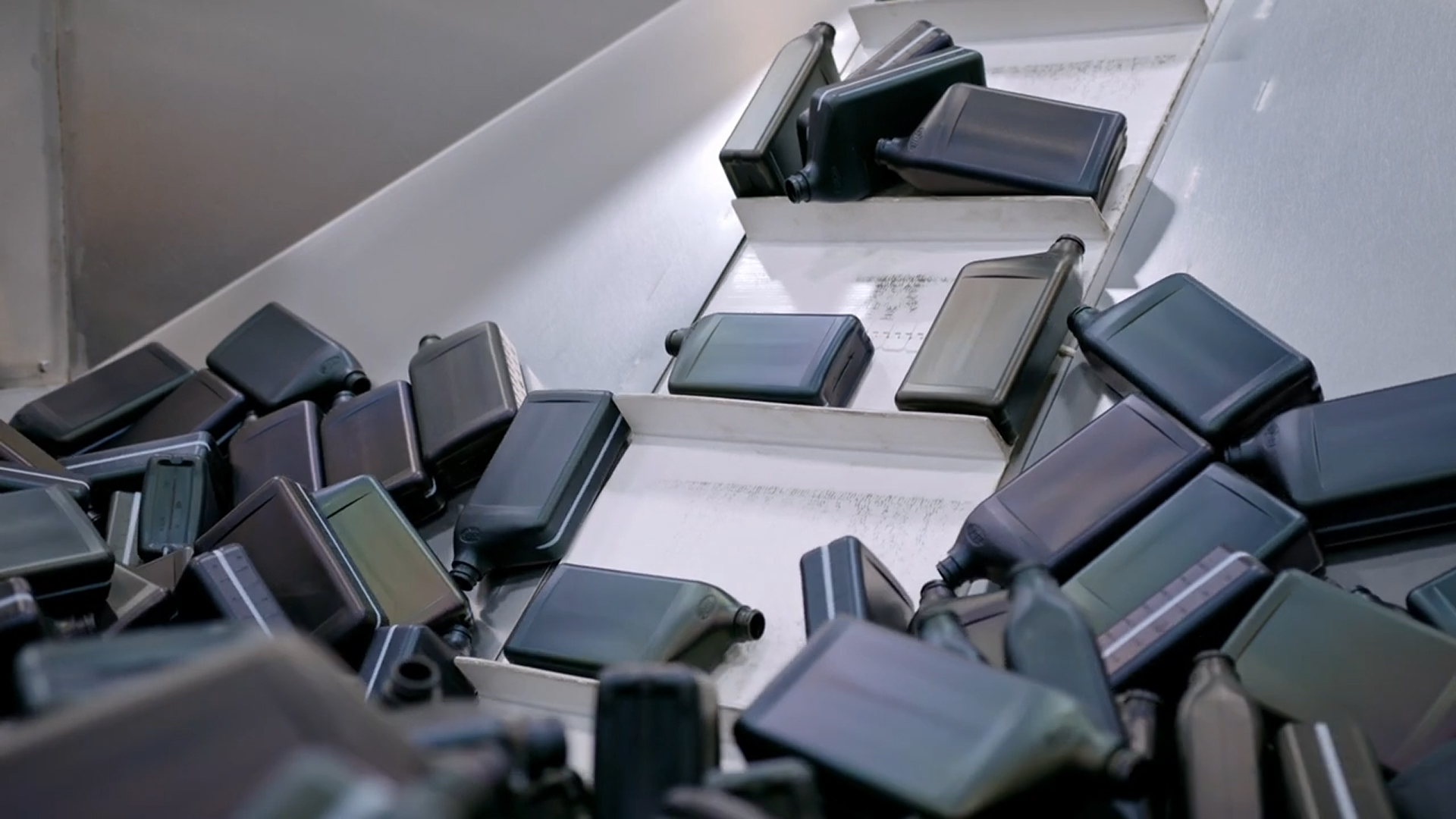
Approach
Purpose-built for classified area requirements
This filling system was designed for a Class I, Division 1 (C1D1) environment—a hazardous location classification where ignitable concentrations of flammable gases or vapors may be present during normal operation. Additional electrical and control measures were implemented to meet these requirements, with particular focus on the filling and capping zones to ensure safe and compliant operation within the classified area.