Jan-San Manufacturing Company
High-speed sanitizing line scales capacity in months
Great Bend, Kansas
2020
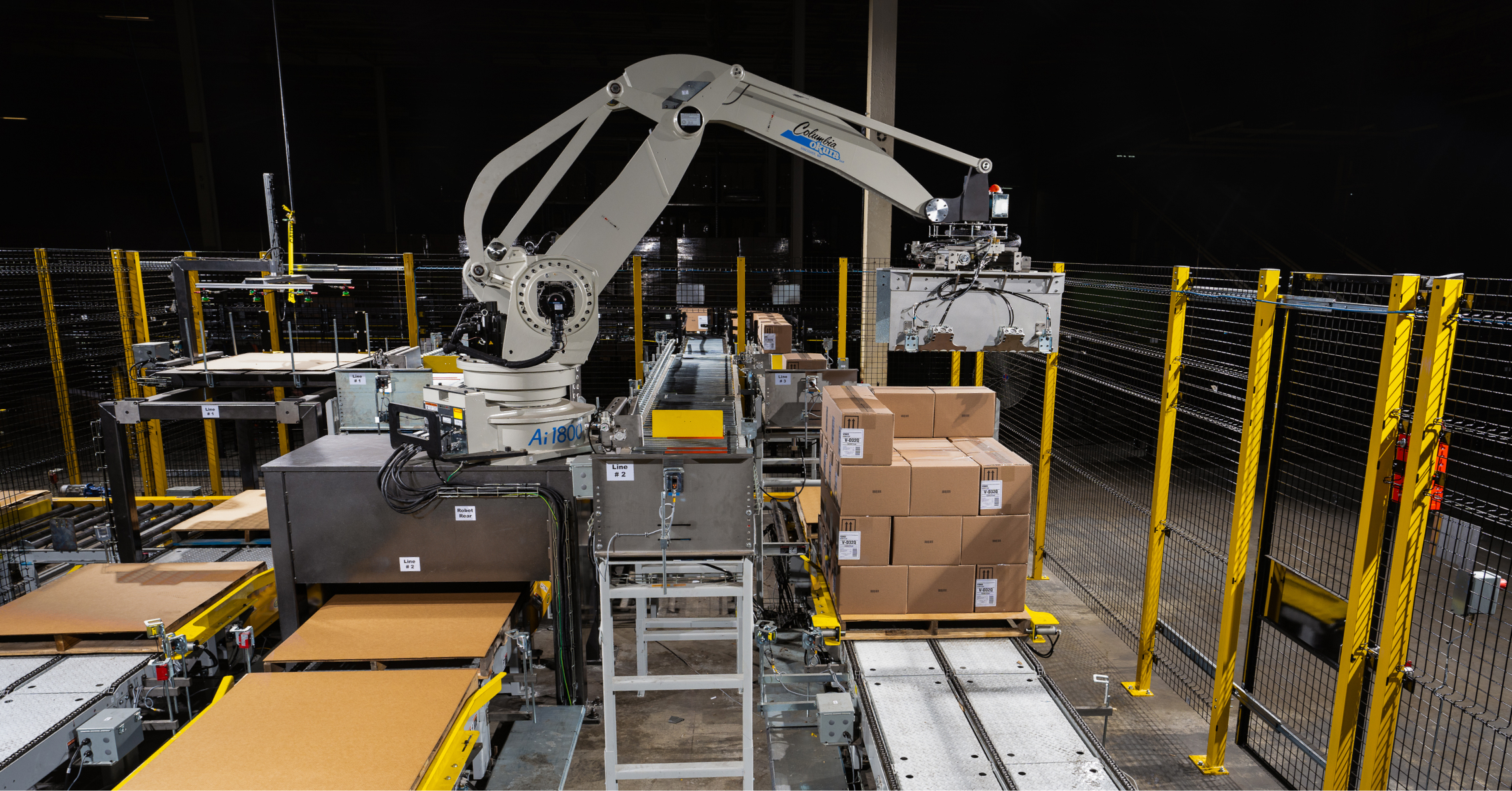
overview
The surge that outpaced manual processes
Equipment Used
Apply-Only Product Labeler
Automatic Stretch Wrapper
Belt-Driven Live-Roller (BDLR) Conveyor
Bottle Unscrambler & Orienter
Case Drop Packer
Case Erector
Case Inkjet Printer
Case Sealer
Continuous Inkjet Printer (CIJ)
Induction Sealer
Inline Bottle Checkweigher
Integrated Control System (ICS)
Lineshaft Case Conveyor
Print-and-Apply Case Labeler
Rotary Filler & Capper
Rotary Pump Inserter
Sortation Conveyor System
Spiral Conveyor
Tabletop Conveyor
Vision Inspection System
This customer was looking to capitalize on the surge in demand for sanitizing products brought on by COVID. Their goal was to build the production capacity necessary to pursue new opportunities in this space and, ultimately, increase the volume and presence of sanitizing products within their overall business portfolio.
The objective was to rapidly design, procure, install, and commission a turnkey liquid filling line with integrated end-of-line automation—on the shortest timeline possible. Speed to market was critical, but so was cost control. The system needed to deliver a strong ROI and present a fiscally responsible investment for stakeholders.
The facility was also experiencing labor shortages, making it essential to implement a solution that minimized operator involvement and reduced manual handling. Additionally, the introduction of a high-speed filling line significantly increased throughput—adding up to 25 more cases per minute to the downstream load. This surge in production quickly overwhelmed manual stacking and stretch wrapping processes.
Automating end-of-line operations became a vital component of the project, ensuring the long-term efficiency of the plant, stabilizing labor demands, and improving overall logistics management.
IMPACT
Key results at a glance
+25 cases/min
While the high-speed line increased demand, the added sortation and palletizing system absorbed the excess production without bottlenecks.
7 → 11 month rollout
Line producing in 7 months; full sortation + palletizing commissioned in 11.
Operators redeployed
Automation cut manual handling to pallet & material replenishment only.
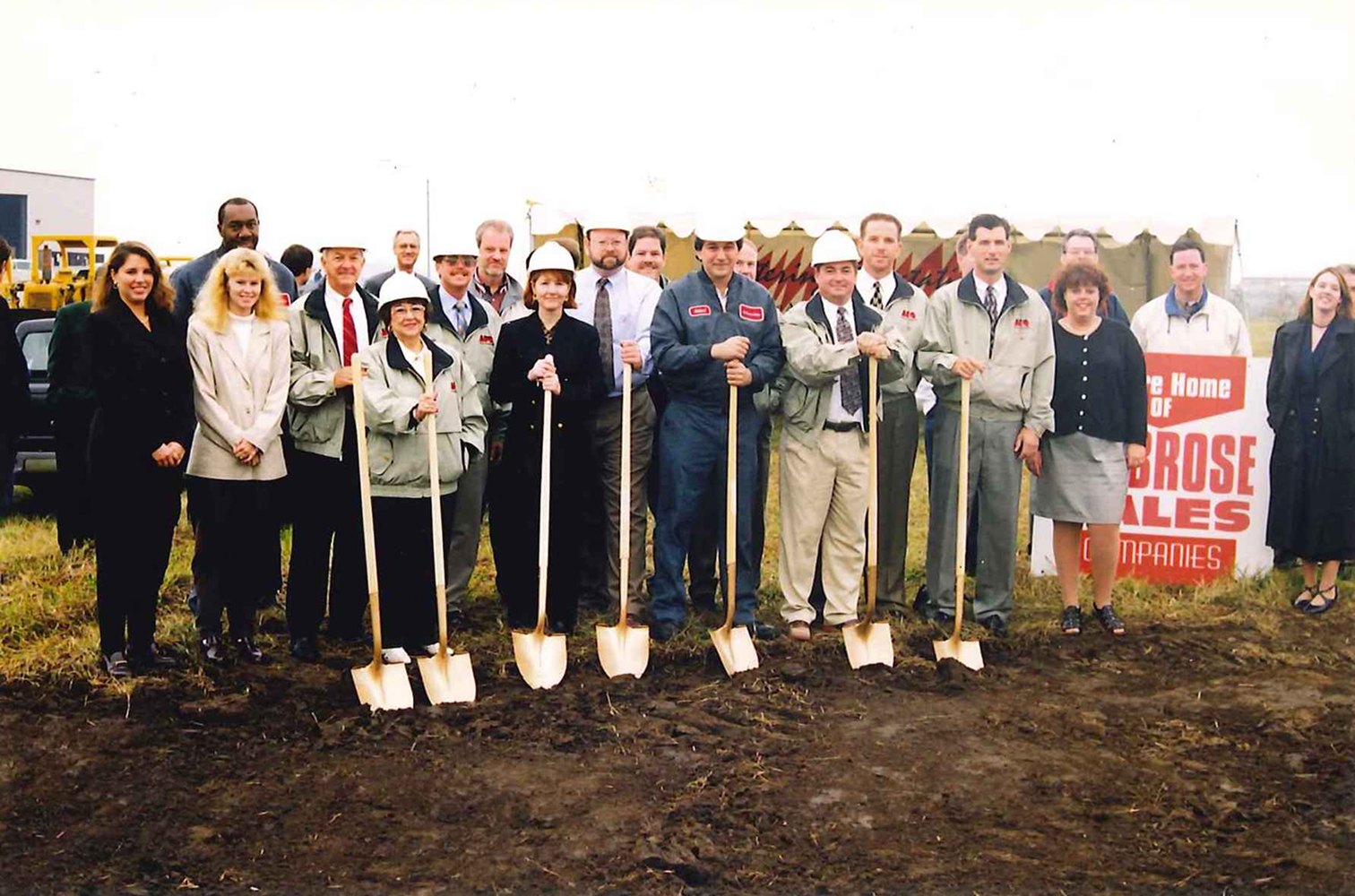
Approach
How we blended speed, ROI, and low-touch automation
Upstream, we designed and integrated a high-speed liquid filling line that conveyed cased goods overhead to a remote section of the facility for sorting, palletizing, and stretch wrapping. This system also supported the infeed of four additional production lines, requiring a balance between the demands of the newly integrated line and the plant’s existing operations.
To enable this level of integration, we implemented a dedicated barcode system applied to each finished case prior to entering the overhead conveyance. These barcodes were read by strategically placed vision systems within the downstream sorting and palletizing cell.
The vision systems identified each case and directed it to the appropriate conveyor path, ensuring accurate distribution to the designated pick stations at the robotic palletizer.
This approach allowed for seamless, automated case management across multiple production lines while optimizing plant flow and reducing manual touch points.