Treated Seed Corn & Soybean Facility
Precise processes for seed bagging line
Elk Point, South Dakota
2024
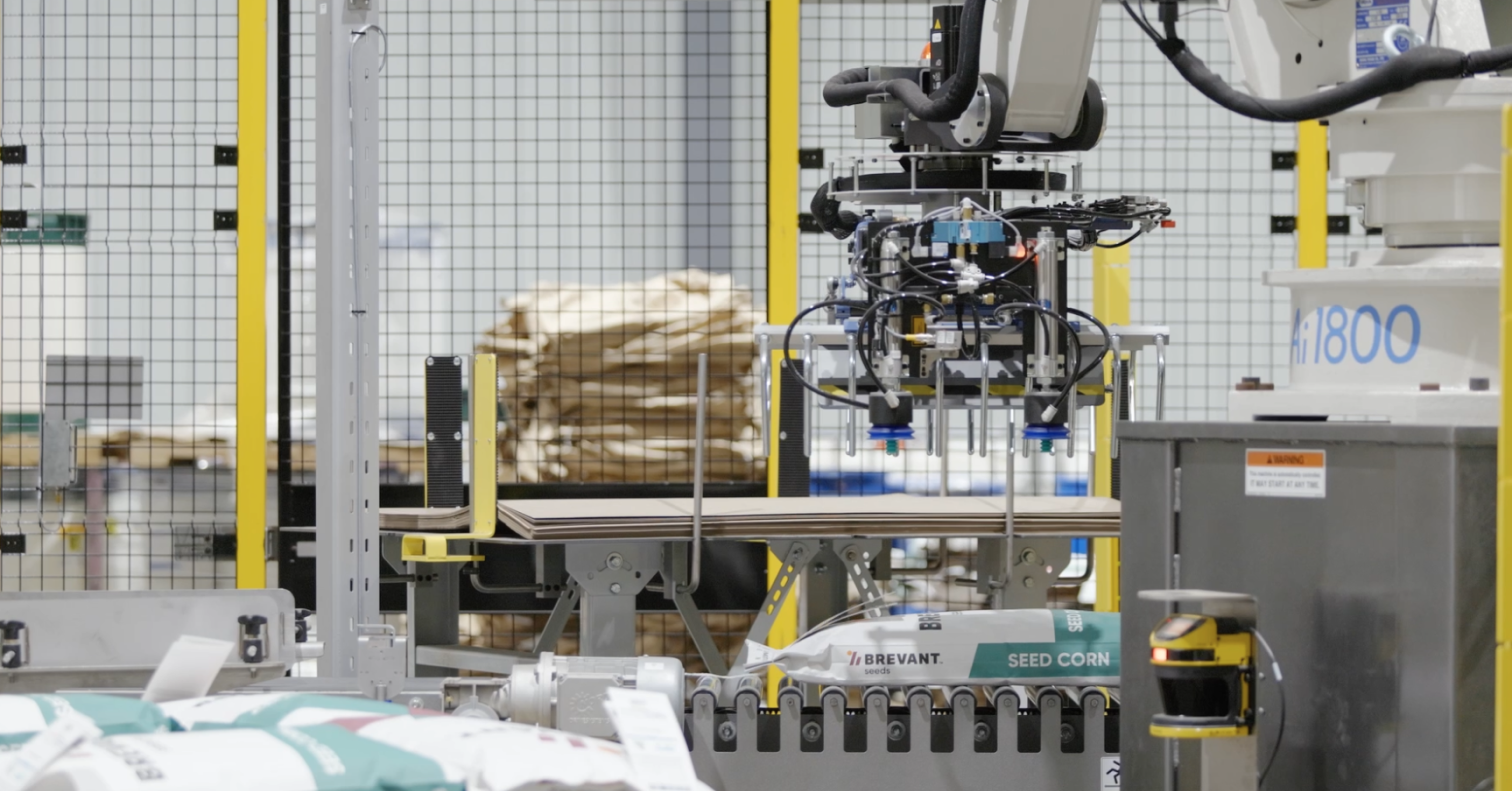
overview
Premium seed corn demands end-to-end precision
Equipment Used
Automatic Open-Mouth Bagger
Automatic Tag Placer
Bag Settling Conveyor
Bagging Scale
Continuous Inkjet Printer (CIJ)
Conveyors & Controls System
Industrial Inkjet Printer
Robotic Palletizer
Sewing System with Tag Infeed
A treated-seed processor needed to elevate both output and presentation quality. At ≈ $300 per 80 K-seed bag, buyers expect perfect seams, collated tags, crisp lip printing, and square pallets. Manual changeovers and inconsistent sewing were limiting rate and jeopardizing appearance standards.
The goal was a fully automatic bagging and robotic palletizing system that could deliver 12 bags per minute while holding tight weight accuracy and flawless tag placement—all inside a new building that lacked reliable CAD drawings.
IMPACT
Key results at a glance
12 bags/min
Automatic line meets target rate with room for growth.
Operators redeployed
End-of-line automation frees staff for higher-value work and positions the plant for larger contracts.
±160-seed accuracy
Every 80 K-seed bag falls within the ±160-seed spec.
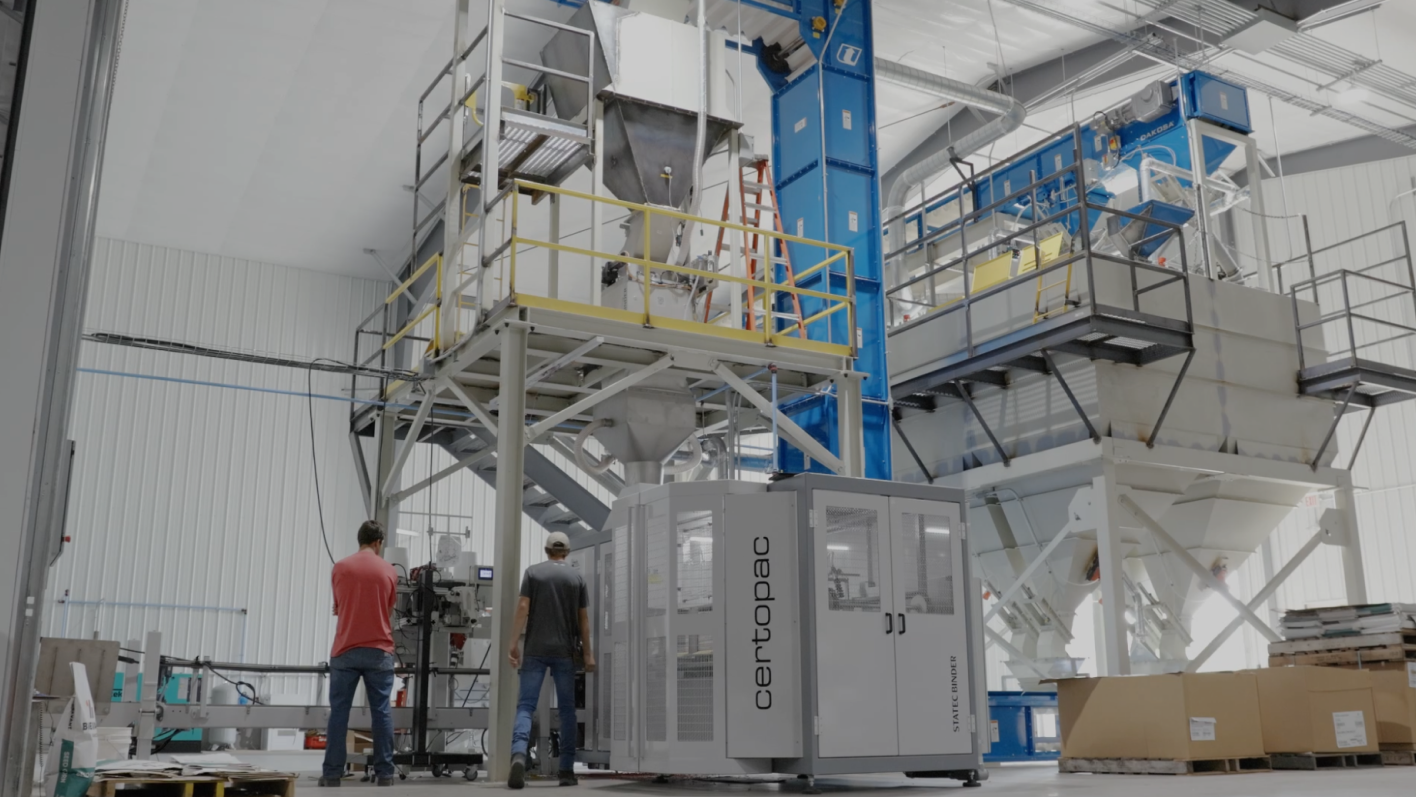
Approach
From CAD to 12-bag/minute performance
We began by laser-surveying the new building and generating AutoCAD drawings, then iterated layouts to maximize space for material replenishment and finished-pallet flow.
Upstream, a servo-driven simplex scale feeds a fully automatic bagging machine outfitted with custom grippers for maximum fill capacity. Filled bags transfer to an in-line sequence of automated modules — tag collation and placement, customized Union-Special sewing, and Squid Ink lip printing—before settling on square-roller conveyors. We engineered the critical hand-offs so each bag moves seamlessly from bagger to tagger to sewer to printer without skewing or jams.
Downstream, a robotic palletizing cell builds uniform, retail-ready stacks that roll directly to shipping. From purchase order to first production, the bagger went live in one week and the palletizer the following week, completing commissioning in just two one-week sprints.