Custom Development and Manufacturing Organization (CDMO)
Robotic palletizing supercharges personal care line
Omaha, Nebraska
2024
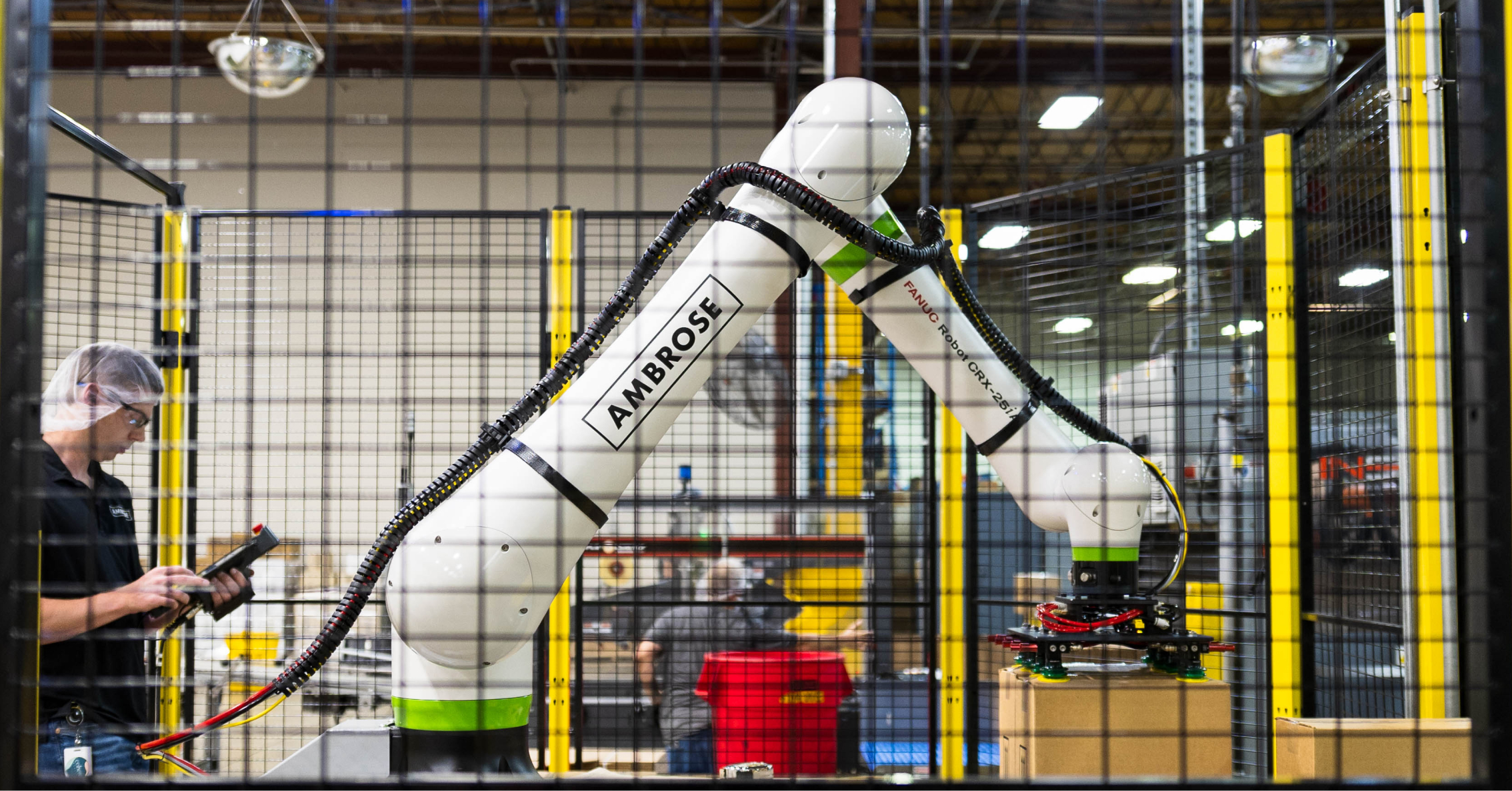
overview
Why manual palletizing had to go
Equipment Used
APS-25 Robot
Custom End-of-Arm Tool
Infeed Conveyor
Reject Conveyor
A leading contract manufacturer of beauty and personal-care products handled finished cases that weighed 40 lbs each. To keep the line moving, operators had to lift those boxes off the conveyor and onto a pallet every 8–10 seconds.
The sustained pace, weight, and awkward reach created significant ergonomic risk—repetitive strain, fatigue, and potential injury—while also tying up skilled workers in a purely physical task. Any slip in placement could compromise pallet stability and slow downstream shipping. The client needed a solution that removed the manual lifts, protected employees, and preserved high line speeds without sacrificing stack accuracy.
IMPACT
Key results at a glance
13.5 cases/min
The robot places 13.5 perfectly aligned cases every minute, matching upstream throughput and removing the palletizing bottleneck.
40-lb lifts gone
Eliminating manual lifts removed a major ergonomic hazard and let two operators move to higher-value quality and line-support roles.
Accelerated lead time
Design, build, FAT, installation, and on-site operator training were completed in just 14 weeks—keeping downtime low and payback quick.
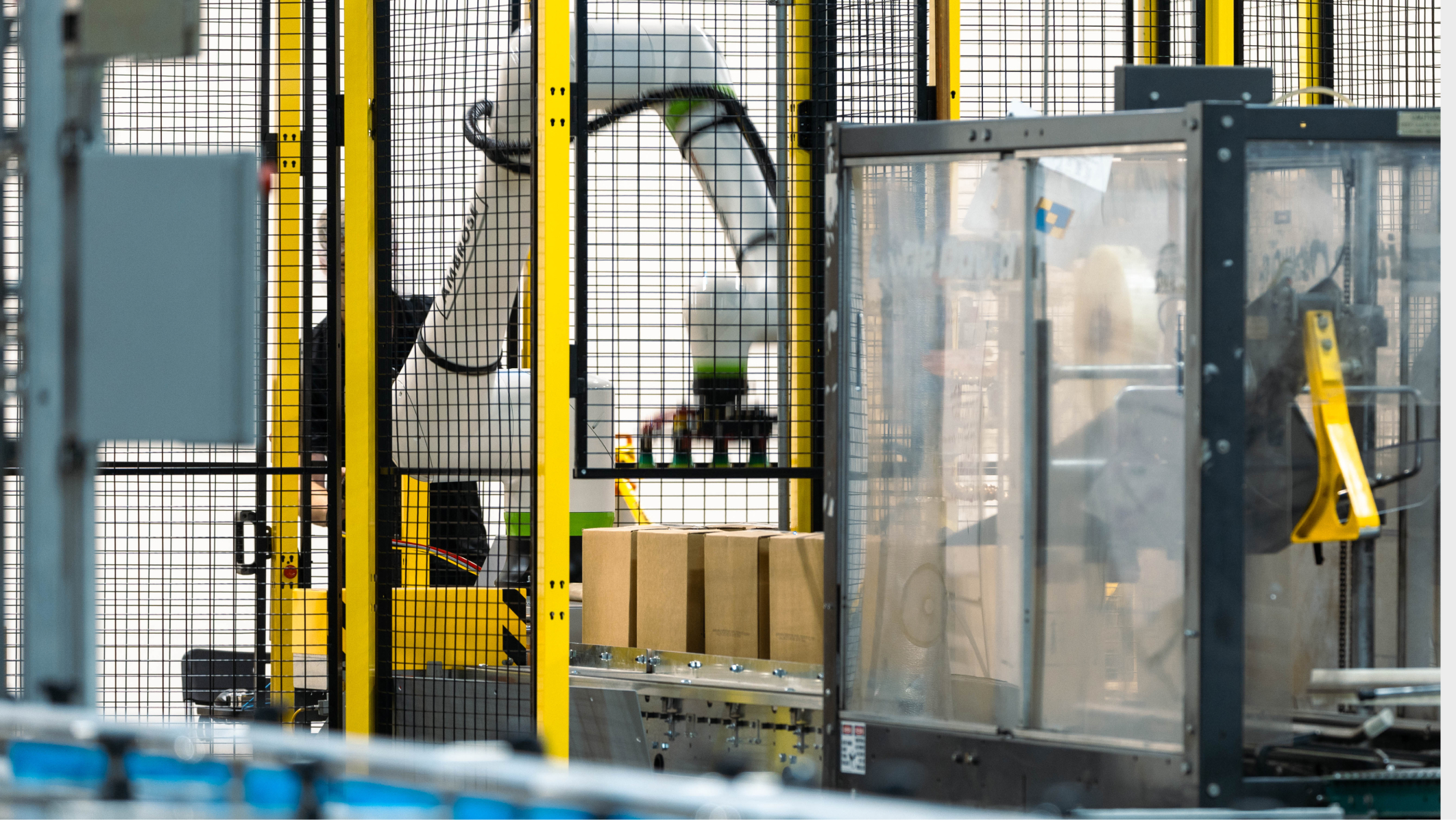
Approach
From design to go-live in 14 weeks
We engineered a turnkey robotic palletizing cell built around a six-axis robot, custom dual-zone end-of-arm tool, and integrated infeed and reject conveyors. The lightweight EOAT grips two tall, heavy cases simultaneously while moving at up to 2000 mm/s, keeping within the robot’s 35 kg payload and maintaining stack accuracy.
To pair high speed with operator safety, we fenced the system and programmed a “speed-switch” workflow: during normal operation the robot runs out of collaborative mode at full speed; when an operator opens the gate to change pallets, it automatically slows, enters collaborative mode, and is constrained by a dual-check safety zone. A vision sensor rejects unsealed cases before they reach the robot, preventing crashes and unplanned downtime.
Our team completed design, build, FAT, installation, and on-site operator training on Fanuc programming in 14 weeks. The cell now frees staff for higher-value tasks, stacks flawless pallets, and requires attention only every 6–7 minutes to swap pallets—delivering immediate ergonomic relief and a measurable productivity jump.